Commit to a Safer Workplace in 2021
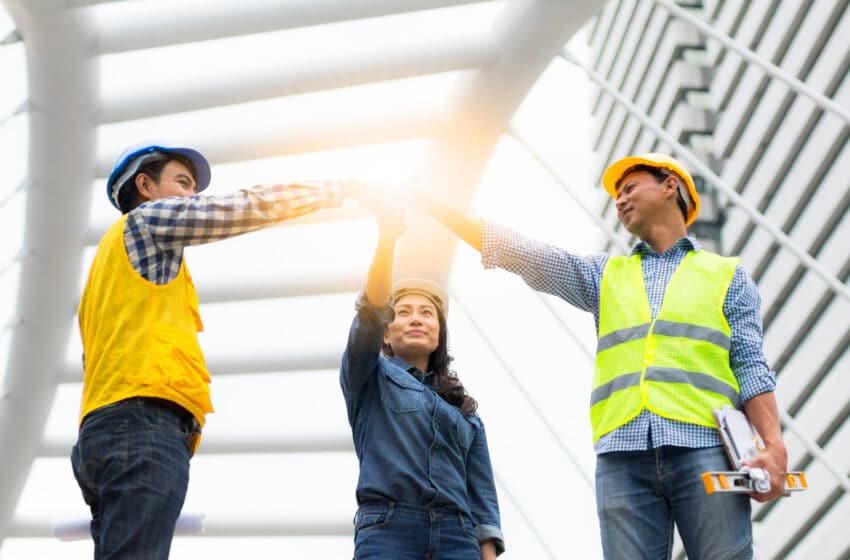
Over the past year, Texas employers have faced extraordinary workplace safety challenges. Use this Plan-Train-Analyze process to create a customized safety program that protects your employees and your business—well beyond COVID-19.
By following these simple steps, you can create a strong plan, develop more effective training measures, and ensure consistency and continuity in your safety practices.
1. Plan
Your safety plan should be customized to meet the unique needs of your company. To help you get started, here are some suggestions for creating a plan that works.
Emphasize safety with your management team.
When your managers value safety, so do your employees.
Issue a clear safety policy statement.
Your people need to understand there is a comprehensive commitment to safety that goes all the way to the top of the company. Put it in writing, and make it available to all personnel.
Designate a point person for your safety program.
Give them real authority to implement your policies. Safety, after all, doesn’t happen by accident.
Commit the resources necessary to implement the safety plan.
Good intentions need to be backed by proper training, personnel and equipment.
Hold and attend safety meetings.
It’s a great way to make information available to personnel at all levels of your company, and it demonstrates your continuing commitment to a safer workplace.
Know how your company works.
Creating a workable safety plan means developing safety rules and procedures that apply specifically to the equipment you use and the type of work taking place. The more familiar you are with the unique tasks of your company, the more reliable you can be in identifying the root causes of potential accidents.
Follow your own rules.
You set the tone for the success or failure of your plan when you and your management team do things the safe way. Provide a model for your employees to follow, make your people aware of your expectations and lead by example.
Seek employee input on the elements of your safety plan.
Nobody knows the equipment better than the people who use it regularly. Ask your employees’ advice when you’re creating the safety program, and you’ll get a more comprehensive plan and a more cooperative workforce.
2. Train
Once you’ve developed your plan, implement a training program that gives your employees the information they need to work safe. These guidelines will help you create the right program for your business.
Train your managers first.
If management doesn’t know your safety procedures and the proper strategies for using equipment, it won’t become part of your employee culture. Managers can ensure that your entire workforce knows and follows the planks of your safety plan.
Make employees aware of the safety aspects of your industry.
It’s not enough that they know their job–they need to know about their job. Inform workers about the potential hazards of your industry, and make sure they know how to use the equipment they’ll encounter. Emphasize the proper use of safety equipment that can lower the risk associated with particular tasks.
Teach your people to think prevention.
Most injuries can be avoided by identifying the situations likely to lead to accidents. What are the causes of injuries in your workplace? Carelessness? Improperly stored equipment? Poor maintenance or housekeeping? By helping your people learn to think prevention first, they’ll be on the alert for unsafe practices and, more importantly, will start looking out for each other.
Train–and train again.
Reinforce your safety plan regularly with updates and reviews. Reinforcement creates a lasting safety routine that sustains your accident-prevention program, even as equipment changes and new employees come on board.
Make sure the training you’re providing is job-appropriate.
Low-risk jobs might need safety reinforcement training quarterly or annually. Higher-risk occupations, on the other hand, might require weekly or monthly training sessions.
Make sure the training is understandable.
Communication is key to training, so avoid making your sessions so lengthy or technical that they lose all meaning. Also, keep in mind the backgrounds of your employees, and make safety training material available in a language they fully understand.
3. Analyze
Analysis and reinforcement are essential to getting the most out of your safety program. Use this checklist to maximize your effectiveness.
Analyze incidents.
Analysis of workplace accidents and illnesses is critical to identifying hidden trends that can impact your safety record. Analyze the data, and be proactive in working to prevent future problems.
Analyze hazards.
Hazard analysis relies on inspection of data with an eye toward eliminating hazards before they cause accidents. Keep track of recurring hazards from past inspections that indicate the need for more training, new processes or improved engineering controls.
Keep records.
This essential step in the safety process provides the necessary documentation to track trends, assess threats to your employees and ensure proper implementation of your plan. OSHA requires companies in many industries to keep accident records. In addition, companies carrying workers’ comp insurance are required to maintain a record of on-the-job injuries. Maintenance records and other documentation may be required, as well.
Inspect.
Conduct self-inspections routinely and regularly with the express purpose of improving workplace safety. Inspections should include routine maintenance, proper use of equipment, behavior of personnel and availability of safety materials. Correct any improper activity, make sure a safe environment is maintained, and document your findings.
Investigate.
If an accident or near-miss should occur, investigate the site immediately and take corrective measures to prevent future occurrences. Interview witnesses and evaluate the worksite to identify specific causes, and then use a standard accident form to ensure consistency in reporting. Finally, alter your training, hiring practices or procedures according to your findings.
Review.
By documenting each step of the process, you’re creating a company-specific guideline for updating and improving your safety plan. Regulations change, as do employees and equipment, so consider new elements when adjusting the plan.
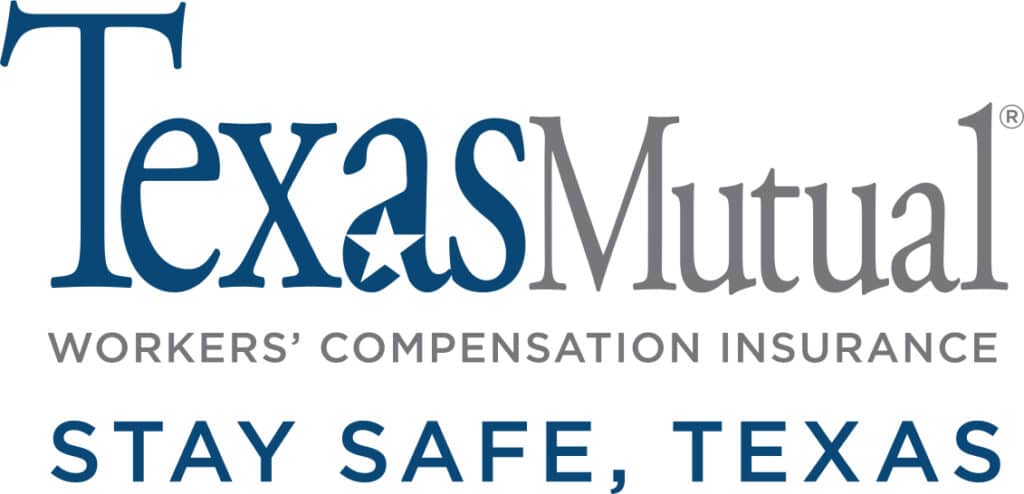
Caring for Texas for more than 25 years
As the leader of the workers’ compensation market, Texas Mutual is committed to building a stronger, safer Texas. We offer workers’ compensation insurance that protects employers, their businesses, and their employees from the consequences of an on-the-job injury or illness. Don’t “go bare”—protect your employees and business with the company that does workers’ compensation bigger and better than anyone else. Whether you work in oil and gas, restaurants, construction, healthcare, auto repair, or any other industry, we’re here to help.
- 70,000+ businesses insured by Texas Mutual
- 8,962 agents across the state, ready to serve you
- 400 self-paced interactive safety courses available to policyholders and their employees